MicroPhysics
Flexible
Magnetic Media Surface Roughness Characterization:
Contact
Interferometry with a Hertz Pressure Loader
Christopher Lacey
MicroPhysics, Inc.
Introduction:
Contact interferometry is a superior technique to
evaluate the surface topography of flexible media.
In this technique, the flexible media is loaded against a transparent
surface under a known contact pressure. The
spacing between the flexible media and the transparent surface is primarily due
to the surface roughness of the flexible media. Under higher contact pressures,
the tape surface becomes smoother and the spacing decreases.
The relationship between contact pressure and average spacing has been
called “tape surface compliance.” Other surface measurement methods such as
non-contact interferometry, stylus profilometry, and AFM are not able to fully
characterize how the media surface behaves as a function of contact pressure.
The purpose of this technical note is to describe a method
for the determination of tape surface compliance. The method is broken into
three parts: (1) the application of known contact pressure to the media, (2) the
measurement of spacing with the contact pressure applied, and (3) the reduction
of spacing information to parameters which indicate the variation of tape
surface roughness as a function of contact pressure.
Throughout this work, “spacing” refers to a value which
is spatially averaged. Although
true contact occurs at the peaks of the media surface roughness, the (averaged)
spacing is typically non-zero.
To determine the compliance relationship, a pressure cell
was constructed using a polyurethane hemisphere to load flexible magnetic media
against a flat glass window. The
contact pressure between the hemisphere and the glass window was calculated
using the theory by Hertz. MicroPhysics
Tape Spacing Analyzer was used to measure average spacing between the tape and
the glass window under a range of contact pressures. A functional relationship between average contact pressure
and average spacing was established by fitting two coefficients using a least
squares technique.
Pressure Cell:
The pressure cell is shown in Figure 1.
Figure 1: Pressure
cell For use with contact interferometer
Flexible media was placed between the glass plate and the
urethane hemisphere. The contact
pressure was applied by loading the hemisphere against the fixed glass plate
using the motorized Z-stage. As the
Z-stage was raised, the force pressing the sphere against the plate increased
and the area of contact between the sphere and the plate also increased.
The load force was measured using the load cell and the area of contact
was measured by observation through the glass plate using the MicroPhysics Tape
Spacing Analyzer as a measuring microscope.
Table 1 gives the area of contact as a function of load force for the
system.
Table 1:
Characteristics of pressure cell
Table 1 also gives the average and maximum pressure
calculated using the theory by Hertz [1,2]. According to the theory by Hertz,
the pressure profile is a hemisphere with the maximum pressure equal to 1.5
times the average pressure.
The maximum contact pressure ranges from 0.48 to 1.61 atm.
This range is considerably higher than the range obtained by stretching
media over a cylindrical contour [3]. The
maximum pressure obtained using that method was on the order of 0.5 atm.
Since the contact pressure at the head/tape interface can be in excess of
1 atm, the measurements made using this pressure cell are closer to the range of
interest than those made by stretching the media over a cylindrical contour [4].
For all measurements in this technical note, the
measurement spot was placed in the center of the contact patch where the
pressure is maximum, and the pressure over the entire measurement area was
assumed to be the maximum pressure. The
validity of this assumption was investigated by calculating the pressure
distribution in the area of measurement. The
measurement area was square with the sides 0.265 mm long.
Figures 2 and 3 show the calculated pressure distribution in the
measurement area for the low and high pressure cases.
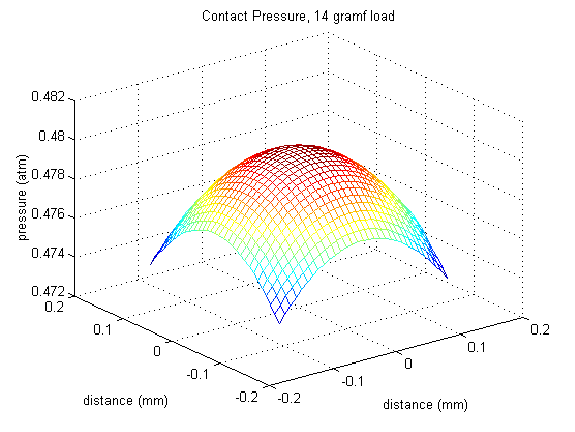
Figure 2:
Calculated pressure distribution for low pressure case
Since the measurement area is small compared to the contact
area, the change in contact pressure over the measurement area is small.
Table 2 gives statistics of the pressure distribution in the measurement
area for these two cases.
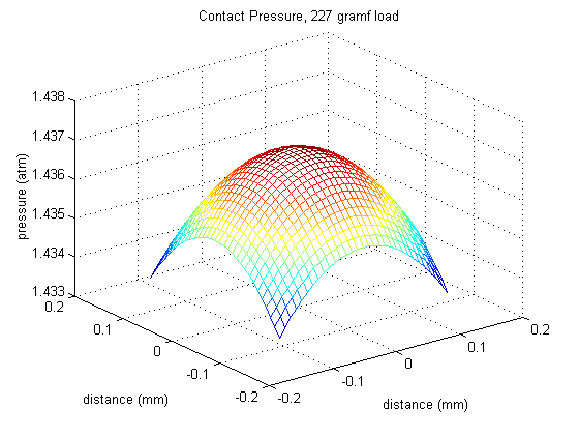
Figure 3:
Calculated pressure distribution for high pressure case
Table 2:
Statistics of pressure distribution
As indicated in Table 2, the contact pressure has little
variation over the measurement area. Therefore,
the maximum pressure was used for all calculations.
Spacing Measurement:
To measure spacing between the flexible media and the glass
plate, the optical techniques of interferometry and ellipsometry were utilized.
The interferometer optically measures spacing.
In order to measure spacing, optical properties of the flexible media are
required. These properties are
measured using ellipsometry. For
the data in this paper, MicroPhysics Tape Spacing Analyzer was for the
interferometric measurements and the ellipsometric measurements were performed
by the Rudolf corporation.
Interferometry:
Microphysics Tape Spacing Analyzer (TSA) is typically used
to measure head/tape spacing by replacing either the head or the tape with a
transparent replica. A diagram of
the system is given in Figure 4.
Figure
4: Two-Color Interferometer
Apparatus
Light leaves the strobe and is
directed to the head/tape interface using a beam splitter.
Multiple reflections occur at and between the head and tape surface.
The light then goes back through the first beam splitter to a second beam
splitter that directs light toward two digital CCD cameras.
Interference filters of a 10 nm bandwidth are used to produce two
distinct wavelengths: one color for each camera. The system controller processes the intensity information
from each camera and feeds the data to the host computer for analysis using
multi-beam interferometric theory with corrections for phase shift on
reflection. Head/tape spacing can
also be measured using real heads in conjunction with transparent tape.
When using real heads, the heads are mounted below the tape rather than
above it as shown in Figure 4.
Interferometric Theory:
Head/Tape spacing is calculated using multi-beam
interferometric theory (Equation 1)[5].
(
1
)
In Equation 1,
r is the amplitude of the external
reflection off the lower surface, s is
the amplitude of the internal reflection off the upper surface, and
is the phase shift between the two
reflected wave fronts.
(
2
)
In Equation (2),
h is the head/tape spacing,
is the wavelength of the light, and
is the phase shift on external reflection.
The values of r, s, and
are typically determined by ellipsometric measurement of the surfaces.
Typical intensity vs. spacing curves for a system with 546
and 633 nm wavelengths are shown in Figure 5.
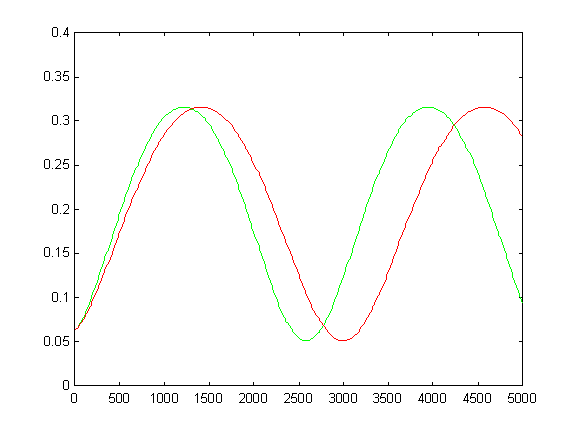
Figure 5: Typical
intensity vs. spacing curves.
One of the most important aspects for the interferometric
measurement of spacing is the calibration of intensity of the detectors.
The purpose of intensity calibration is to find scale and offset factors
that can be used to transform the output from the digital camera into the
normalized intensity units of Equation 1. To
calibrate intensity, a number of interferometric images are captured while
slowly varying the spacing. The
spacing must vary so that an interferometric minimum and maximum pass by each
pixel of the measuring cameras while they acquire images.
The images are analyzed to determine the maximum and minimum
interferometric intensities that were recorded during the calibration process. The measured maximum and minimum are compared to the
theoretical maximum and minimum of equation 1 and offset and scale factors are
calculated for each pixel on each of the detectors.
These offset and scale factors are used to transform the camera output
into the appropriate units for application of equation 1.
When the spacing is determined by application of Equations 1
and 2, the spacing can be determined
independently by each color. Due to
system imperfections, the spacing measurements determined by each color can be
different. If the difference
between the two measurements is greater than a pre-specified tolerance, the
spacing measurement is rejected, otherwise, a degree of confidence is assigned
to the measurement.
Ellipsometry:
The phase shift on reflection and the reflectance of the
flexible media were determined by ellipsometry. Four samples of magnetic tape were measured.
The results are shown in Table 3.
Table 3:
Optical Data for Various Magnetic Tapes
In Table 3, ps is f
and ref is r.
The values for n and k were obtained from
the ellipsometer assuming the flexible media to be an isotropic bulk medium.
The values for f
and r were calculated from n
and k using equations given in reference [5].
The in-line test cases had the machine direction of the
magnetic tape in the plane of the light used for ellipsometry.
The transverse cases had the tape rotated 90 degrees (Figure 5).
The differences in the measurements for the two cases are indicative of
imperfections in the assumptions used to reduce the data, in particular, that
the media is homogenous and isotropic. For
determination of spacing, the average values were used as shown in the last two
columns of Table 3.
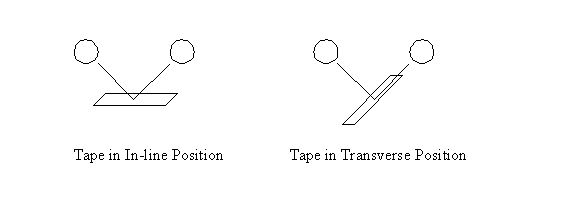
Figure 5: Transverse and in-line tape orientation in ellipsometer
Spacing Measurement in Pressure Cell:
To perform the spacing measurements for flexible media
surface characterization, MicroPhysics Tape Spacing Analyzer (Figure 4) was used
with the Hertz pressure cell (Figure 1) substituting for the tape looper.
Measurements:
Measurements of average spacing in the pressure cell were
made for four samples of each of the four different tapes. The spacing measurements were made using a 111 by 111 pixel
area of each measurement camera. This
area corresponds to a square with 0.265 mm long sides on the surface of the
tape. The average spacing data is
reported in Table 4.
Table 4: Average
Spacing Measurements
Each average spacing measurement consists of the average of
12,321 pixels of data in the area of interest.
The standard deviation of the spacing data for each measurement was also
recorded. The standard deviation
data is reported in Table 5.
Table 5: Standard
deviation of spacing measurement data
In all cases, the average spacing and the standard
deviation of spacing decrease as the pressure increases.
Fitting parameters to the data:
The average spacing data was fit to Equation 3
(3)
where h is the
average spacing,
is the contact pressure normalized
to sea-level atmospheric pressure, and
and
are fit parameters.
Since
generally has a value between zero
and negative one, this equation has hyperbolic characteristics, i.e. it
approaches but does not intercept either axis.
For the purpose of communication and reporting the fit
parameters, two other parameters are used:
and
. The parameter
is the spacing at 0.1 atm of
contact pressure. Parameter
is the spacing at 1.0 atm of
contact pressure. Transformations
between
,
and
,
are giving in the following
equations.
(4)
(5)
(6)
The parameters
and
are both expressed in units of
length; they can be easily transformed to different systems of units and their
interpretation is straight forward.
Values of
and
for the four tapes are given in
Table 6.
Table 6: Surface
compliance parameters for various magnetic tapes
The standard deviations for the measurements were generally
below one nanometer, indicating not only that the measurement technique was very
repeatable, but also that the surface roughness of the tapes was very uniform.
One exception to the uniformity was the M2 tape which appeared to have
small particles on the surface causing increased non-uniformity between
different measurement samples.
Data Images:
Contour plots of spacing are given in Figures 6-9.
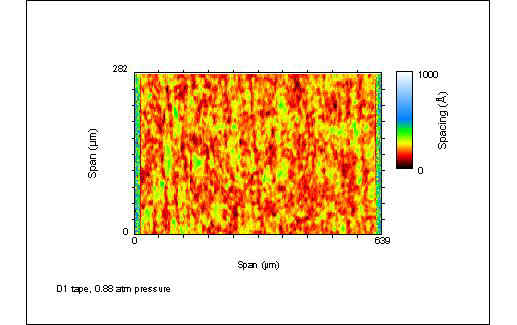
Figure 6: Spacing
for D1 tape at 0.88 atm.
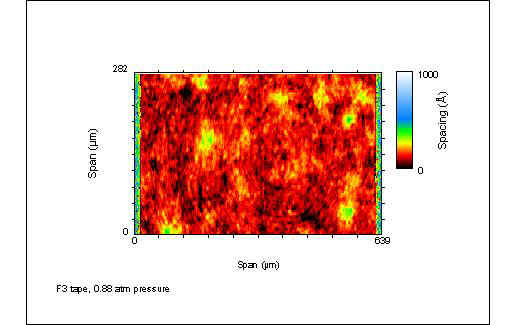
Figure 7: Spacing
for F3 tape at 0.88 atm.
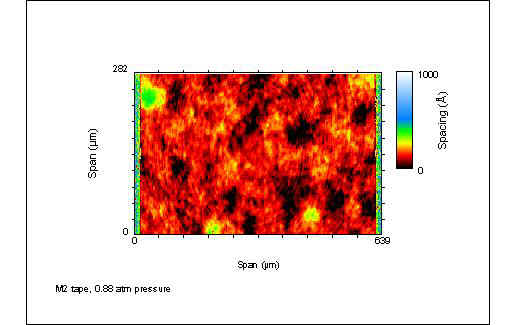
Figure 8: Spacing
for M2 tape at 0.88 atm.
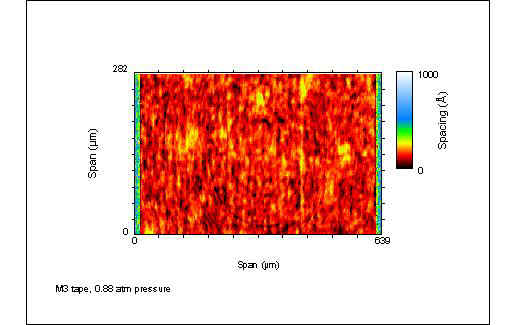
Figure 9: Spacing
for M3 tape at 0.88 atm.
Summary:
This document describes a method and apparatus for the
characterization of surface roughness of flexible media.
References:
[1] Burr, Author H., Mechanical Analysis and Design,
Elsevier, New York, 1983.
[2] Smith, David P., “Contact and Pressure Relationships
of Polyurethane Hemispheres on Glass,” Unpublished Technical Note of 3M Data
Storage Tape Technology Division, St. Paul, 1995.
[3] Lacey, C.A., and Talke,
F.E., “Measurement and
Simulation of Partial Contact at the Head/Tape Interface,” Transactions of the
ASME, Journal of Tribology, Vol. 114, October, 1992
[4] Wang, Erik L., Wu, Yiqian, and
Talke, Frank E., “Tape
Asperity Compliance Measurement using a Pneumatic Method,” IEEE Trans. Mag.,
Vol. 32, No. 5, Sept. 1996.
[6] Anders, Thin
Films in Optics, The Focal Press, London, 1965.
Specifications subject
to change without notice or obligation.
Copyright © 1999-2020 MicroPhysics, Inc. All Rights Reserved.